Finders, Keepers, Printers
We may be a small team but here at Haath Paper, we have big dreams. Among them is to master the art of printing using a letterpress machine, maybe even own one. Acquiring a letterpress machine is no small feat, especially that they’ve become antiquated and harder to find, even more so resources for repairs. We juggled our tireless search for a letterpress machine with a resolute mission to learn how to operate it on our own. All our hard work paid off on a rather balmy day in June 2021 when we finally got our hands on a beautiful Chandler & Price Old Style Press. We decided to call her Billie, and we spent the rest of the day learning about her from the previous owner.
We worked on Billie’s restoration at once and while she has been around for a century, we’re extremely fortunate that she didn’t have a lot of missing parts and that we were able to restore her to a functional state. Still, a letterpress restoration project wasn’t easy. Billie showed apparent signs of age, a need for extensive detailing, and a thirst for a fresh coat of paint. But after watching a string of tutorial videos, braving through trials and errors, and commissioning the help of skilled family and friends, we were able to give Billie a makeover reflective of her prestige. We also gave her a wooden tabletop made of scrap narra and palochina wood to facilitate printing and to add a touch of balance to her mostly metallic make.

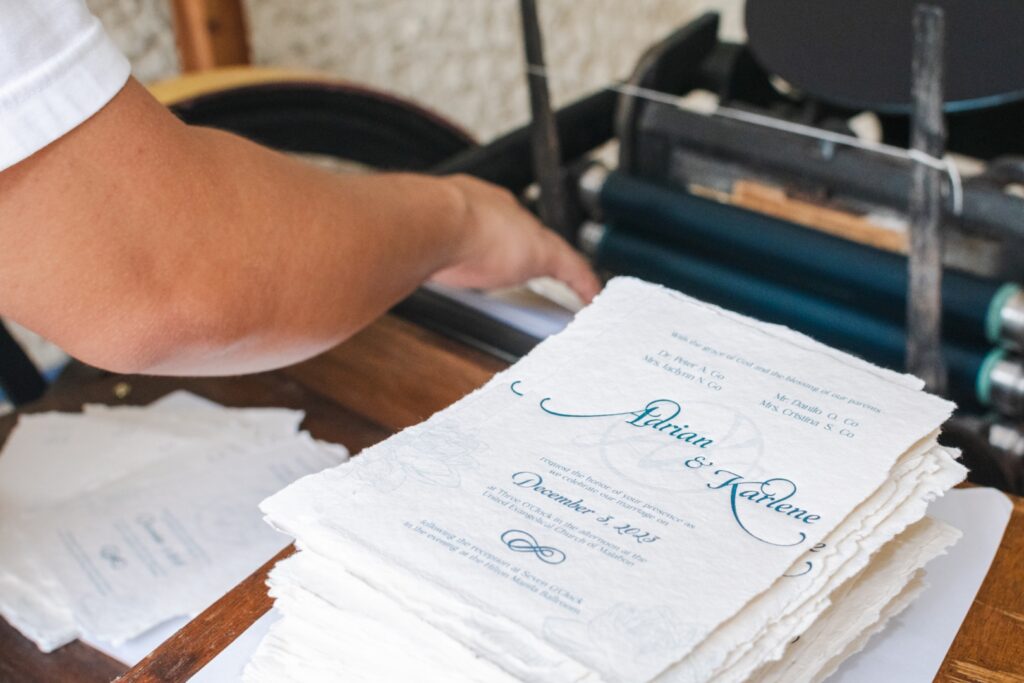
This is where the magic happens
At times we feel letterpress printing is a little too beautiful for words but we take a shot and give you a quick narrative. We begin by creating the metal printing plate (some use polymer) of the design and then we set the press. When the printing plate is ready, we register it carefully on the chase base and then set it into the letterpress machine. This custom plate is what we’ll use to transfer the design to the paper.
We also mix the ink ourselves, an exercise in color theory and an even more stringent test of patience and familiarity with the Pantone Color Formula Guide. Although some color variation is possible, we aim to achieve a flawless shade match with every ink we create. It is also a part of our process to run test prints; this way, we’ll be able to gauge whether the ink is just right or requires adjustment and if the alignment and registration are in place.
When the ink is ready, we apply it to the ink disk and place it on the printing press. With the help of the machine’s rollers, the ink is evenly distributed on the disk, preparing it for application onto the metal printing plate. We then place a sheet of paper on top of the platen and run the press—this forces the inked metal plate onto the paper, creating an impression of the design. Our meticulous printing process follows a one-sheet and one-color-at-a-time procedure to ensure that every print is crisp and every stroke of type has character.
Letterpress as love language
Working with Billie taught us that letterpress printing is a labor of love, the kind that is unrushed because every step is as delicate as the handmade papers we use. When you print using a letterpress machine, you get to indulge your fingertips to the luxurious tactile quality of every print. It is also a more intimate way to create prints as the machine is fed with paper by hand sequentially and with utmost care, making each print timeless and unique. Finally, printing with a letterpress is kinder to the environment as it requires less ink, incurs minimal waste, and runs on less energy.
Our work at Haath Paper and Billie gave us a terrific opportunity to preserve the tradition of letterpress and share the art we create through it with fellow lovers of paper, printing, and everything in between. Send us a message today and learn how we can help you create a host of beautiful prints with our handmade papers and our trusty letterpress printer, Billie.
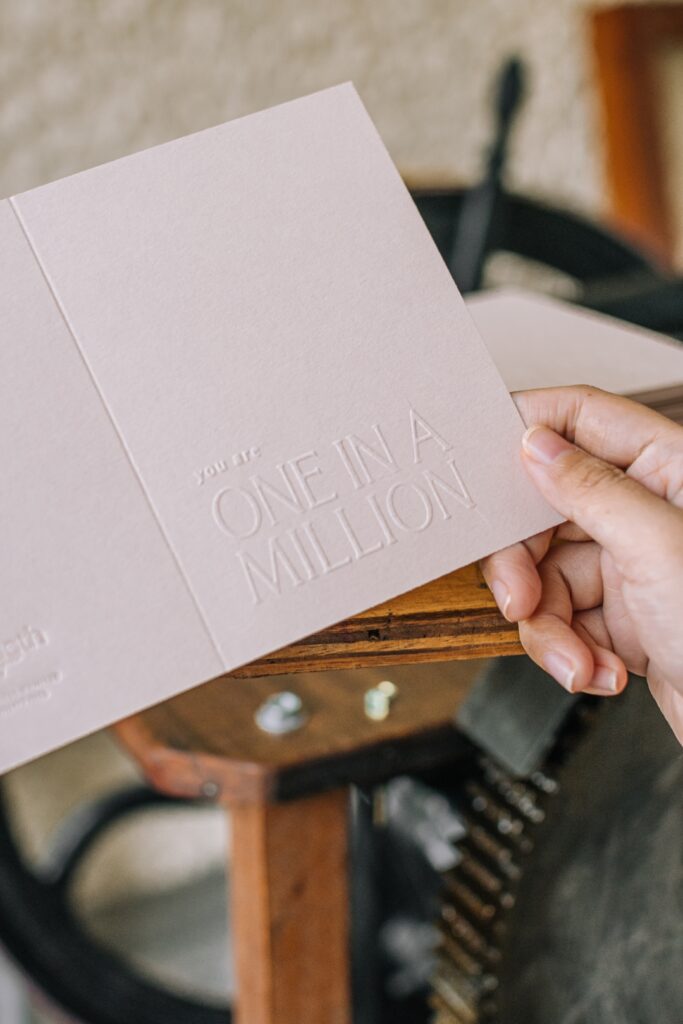